Wicks That Whisper: A Life Of Production
- Nathaniel Boulard-Patterson and Tamara Thompson
- Nov 21, 2020
- 4 min read
Week 7
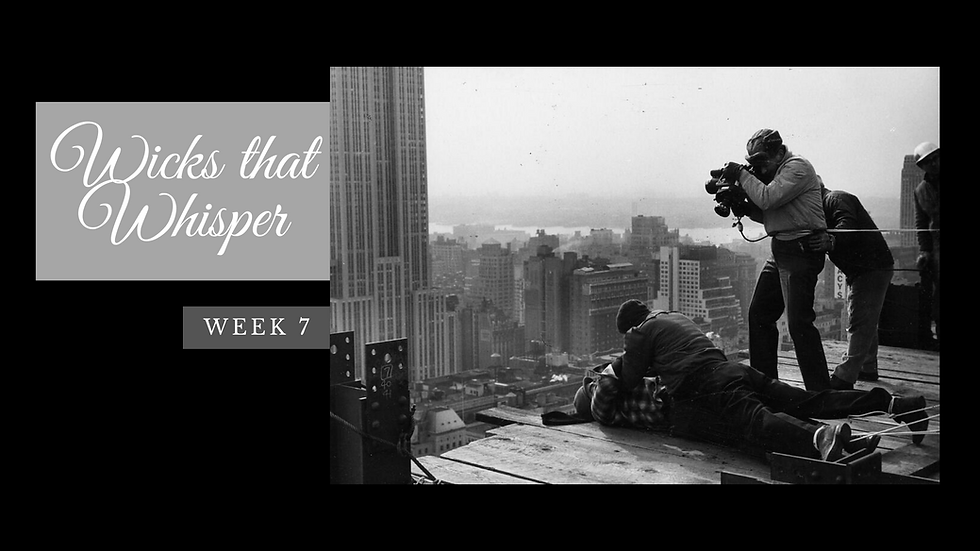
This week we were all hard at work for our next launch, but you all knew that already. So, for this week we thought we would give you a special look into how our production team created our unique chapbooks. We can’t go into all the details, but we thought it would be a fun thing to share with all of you what we can as many of you might not know how chapbooks are made. All presses have their own way of making their chapbooks and their own style, and this is how we made ours. We hope you enjoy this week’s blog insight into our production process.
When planning to create something physical, the first thing one needs to contemplate is the materials needed to do so. That being the case, we began by planning both the materials we would need and the specific type and styles we would prefer. Going through online stores to compare prices and available stock, we drafted a list. Now, like anything else, things don’t always go according to plan and that is exactly what happened when we finally went out to purchase our materials. Not only were we required to drive all over town, some stores lacked the items we needed and wanted and so we had to make do with suitable substitutes. You might be thinking that this isn’t so bad, but when you consider how difficult and stressful it is nowadays to even leave one’s house with the pandemic going on, setbacks like these can be utterly exhausting. So frequent breaks are required.
Once we finally acquired all our physical materials, the next big step was to actually begin printing. Again, you might think this would be an easy task, but when using a printer that you’ve never laid your hands on before to print products it has never been used for before, hiccups are bound to happen, and let us tell you, they did. We started with some test prints in order to ensure that the actual sold product would look nice, alignment was correct, and the ink set right. This probably took about half a day to a full day to make sure we got everything just right. However, once we got the ball rolling, we hit another wall when the printer kept overheating due to the sheer volume of pages being printed. Adapting once more, we began printing in chunks, allowing our printer to take the breaks it very much needed. This process took a long time and ate up a little more time than originally planned.
Once we had our books, it was actually a quick process. David would punch holes into the books for binding. We originally wanted an awl but were unable to find one and the closest thing we could find was a belt loop puncher, so we used that instead. This required a rubber mallet hammer to work and a bit of force. It worked out well all in all. He’d measure out where our holes needed to be, then hammer them out with relative precision. Covers and pages would be punched together, except those for Rebecca’s book as she made custom covers. Instead, we would hammer the pages first then line them up with the cover to ensure the holes were in the right place and hammer the cover separately.
When the holes were finished, another team member would fold the pages and bind them with the chosen embroidery thread. We would then press the books to help make sure they could fit properly in their packaging. With Rebecca’s covers, once more, as they were unique, they did need to be cut due to them being slightly too large. Once pressed, they were ready to ship out to everyone who wanted one! Mailing them was as simple as mailing a letter.
David specifically states:
“It was almost strange to see something the whole team had been working towards finally come to life. There was a moment in the process where I realized what I was doing. Guess you get so caught up in getting everything done that when you start to assemble them it hits you. You have finally slowed down and actually get a moment to really think about it. “
Learning this type of production has been a process for our entire team and as we embark on repeating the process once more in the coming weeks, we hope things run just a bit more smoothly than they did before as we now have some experience under our belts, though we believe that the shocking moment when we realized exactly what it is we’ve created will never fade no matter how many times we finish a print run, as every book we have and will create will continue to be unique in its own way.
We hope you have a wonderful weekend and we send you off with another weekly dad joke from our editor.
“A steak pun is a rare medium well done.”
Comments